Unveiling the Craft of Glass Bottles: A Journey from Raw Materials to Finished Products
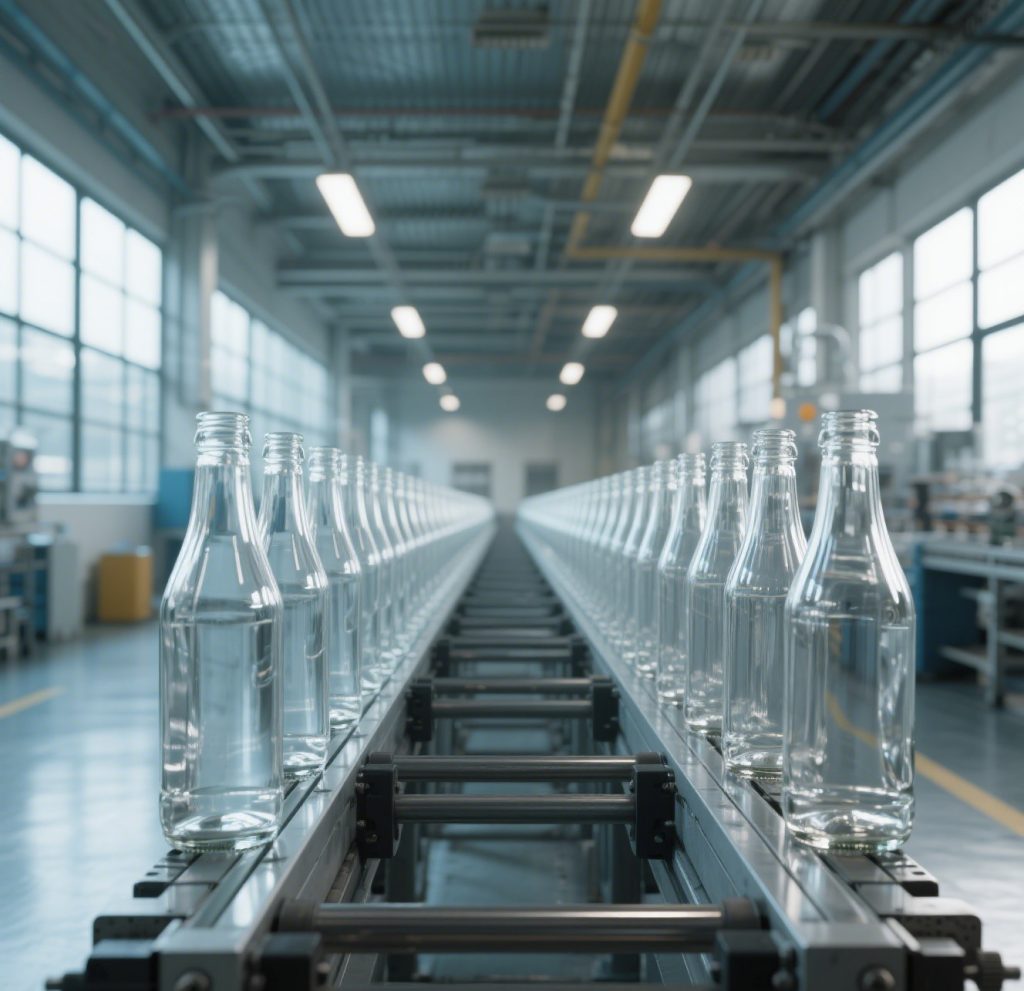
Glass bottles are ubiquitous in daily life—whether as transparent perfume containers, sealed jars filled with jam, or beverage bottles holding refreshing drinks. Their translucent texture and diverse shapes have become an integral part of our lives. But do you know how these glass bottles transform from a pile of raw materials into practical and aesthetically pleasing containers? Let’s delve into the unique craftsmanship behind glass bottles.
1.Raw Material Selection: Laying the Foundation for Quality
The main raw materials for glass bottles are quartz sand, soda ash, and limestone. Quartz sand is the primary component forming the glass, with its purity and particle size directly affecting the transparency and stability of the glass. Soda ash lowers the melting point of quartz sand, allowing the raw materials to melt into glass liquid at a lower temperature. Limestone acts as a flux and enhances the chemical stability of the glass. To meet different usage requirements and aesthetic effects, auxiliary materials are often added, such as colorants to give glass bottles vibrant hues, fining agents to eliminate bubbles in the glass melt, and fluxes to accelerate the melting process.
For example, when producing pharmaceutical glass bottles, the purity and safety of raw materials are extremely critical. Strict screening is necessary to ensure no harmful residues that could affect drug quality. In contrast, when crafting artistic glass bottles, special metal oxides may be added as colorants to create gorgeous and colorful, uniquely artistic visual effects.
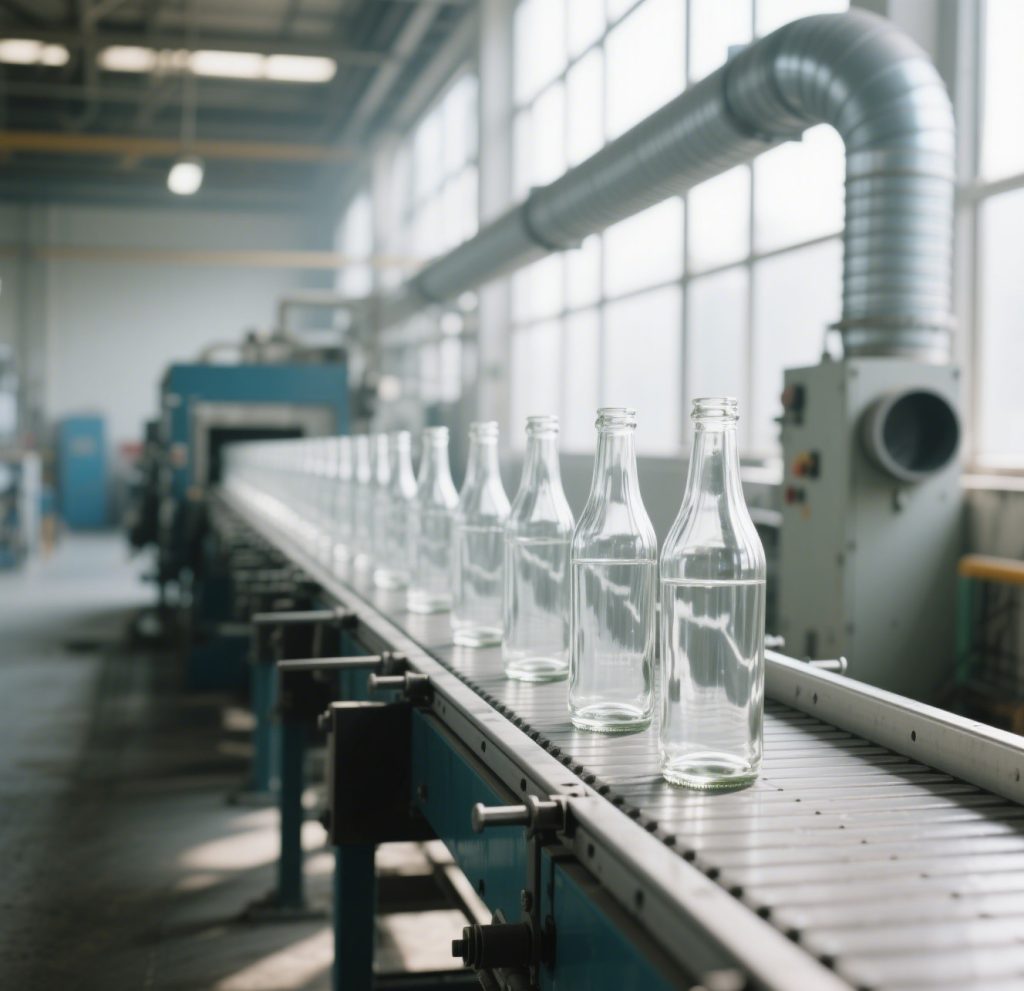
2.Melting Process: Magical Transformation at High Temperatures
After mixing the selected raw materials in a certain proportion, they are fed into a high-temperature furnace. The temperature inside the furnace typically reaches 1500°C to 1600°C. At such high temperatures, the raw materials gradually melt and undergo complex physical and chemical reactions, eventually forming a uniform, bubble-free glass melt.
To ensure the quality of the glass melt, the furnace must precisely control temperature, pressure, and atmosphere. Advanced furnaces adopt all-electric melting technology or regenerative combustion technology, which not only improves energy efficiency but also better controls the composition and quality of the glass melt. Meanwhile, the glass melt needs to be continuously stirred during the melting process to fully mix all components and avoid local unevenness.
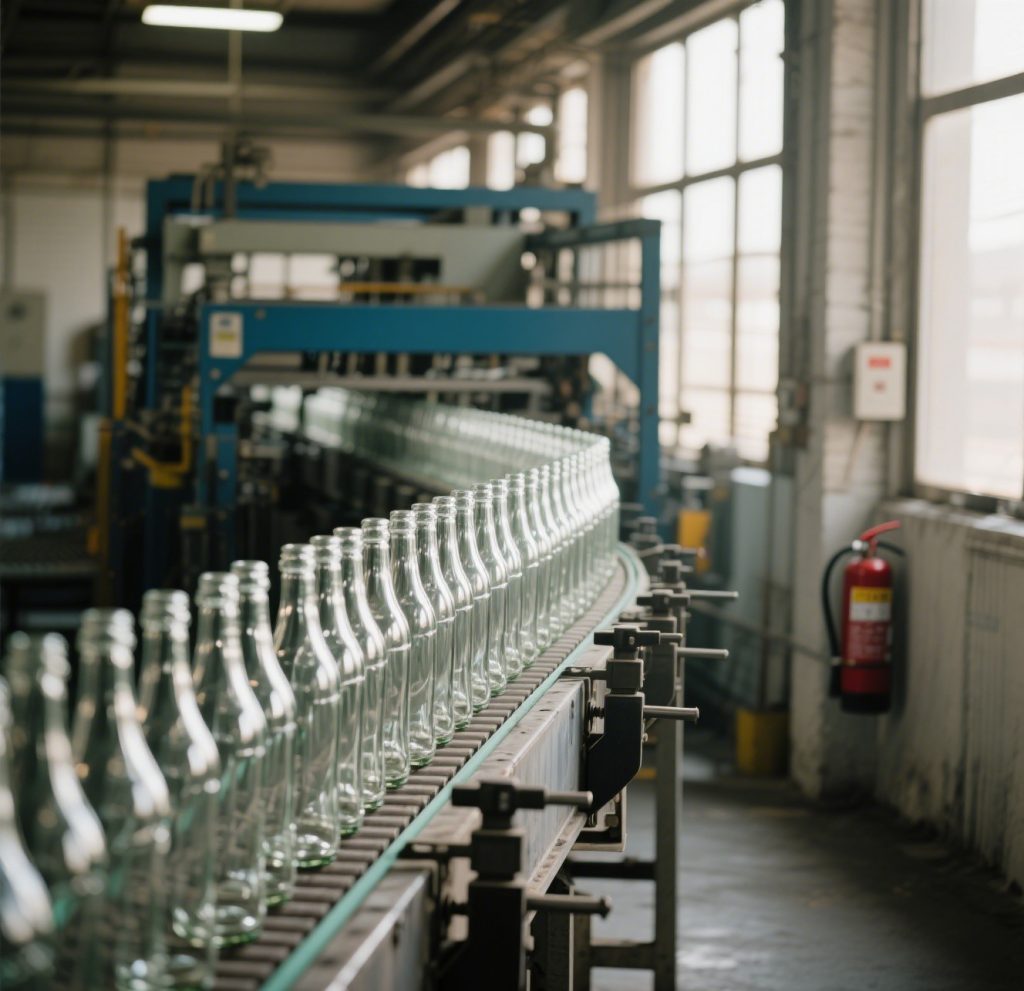
3.Shaping Techniques: Endowing Unique Forms
(1) Blowing Process
The blowing process is a common method for forming glass bottles, divided into hand blowing and mechanical blowing. Hand blowing requires craftsmen to have superb skills and rich experience. They pick up the high-temperature glass melt at one end of a blowpipe and shape it into various forms through blowing and manual modeling. This method is suitable for producing personalized, artistic glass bottles, such as hand-blown glass vases and glass crafts.
Mechanical blowing uses automated equipment to blow the glass melt into the desired shape through molds and mechanical devices. Common mechanical blowing methods include the IS (Individual Section) machine blowing and press-blowing. IS machine blowing is highly efficient and suitable for mass-producing standardized products like beverage bottles and beer bottles. The press-blowing method first presses the glass melt into a preform, then further shapes it by blowing, capable of producing glass bottles with high dimensional accuracy and uniform wall thickness, often used for making cosmetic bottles and pickle jars.
(2) Pressing Process
The pressing process involves placing the glass melt into a mold and forming it under pressure. This method is highly efficient and suitable for producing glass bottles with simple shapes and thick walls, such as perfume bottle caps and glass ashtrays. During pressing, the design and manufacturing precision of the mold play a crucial role in product quality—high-precision molds ensure the dimensional consistency and surface finish of glass bottles.
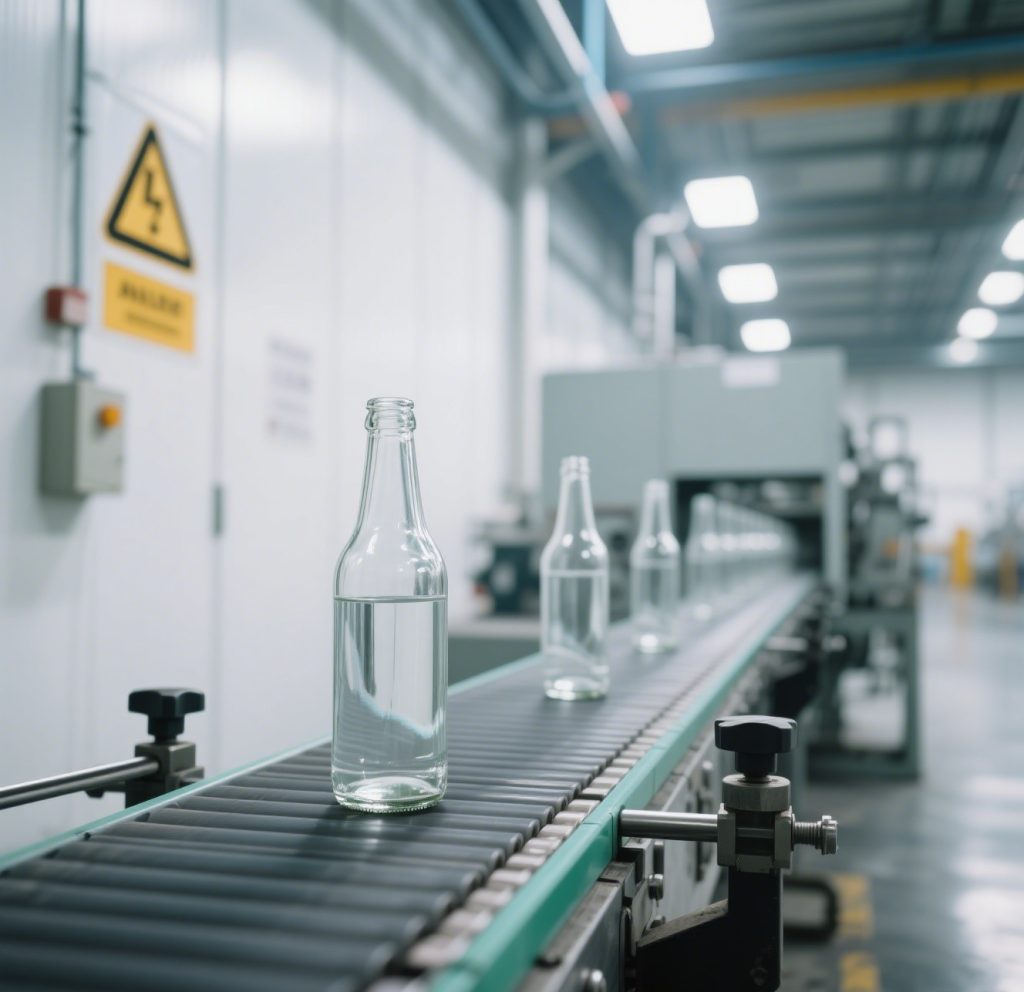
4. Post-Processing Steps: Enhancing Quality and Aesthetics
(1) Annealing Treatment
After forming, glass bottles have significant internal stress. If left untreated, they are prone to cracking during subsequent use. Annealing treatment involves heating the glass bottles to a certain temperature and then slowly cooling them to eliminate internal stress, improving the strength and stability of the glass bottles. The temperature curve and cooling rate of the annealing process need to be precisely controlled, and the annealing parameters vary for different types and thicknesses of glass bottles.
(2) Surface Treatment
To enhance the aesthetics and functionality of glass bottles, surface treatments are often applied. Common surface treatment methods include sandblasting, coating, and printing decoration. Sandblasting gives the glass bottle a hazy texture, increasing artistic effects, and is often used for cosmetic bottles and high-end wine bottles. Coating treatment can form a thin film on the surface of the glass bottle, improving its barrier properties to prevent the contents from oxidation and deterioration, while also increasing the gloss of the glass bottle. Printing decoration uses screen printing, thermal transfer, and other technologies to print exquisite patterns and text on the surface of the glass bottle, serving as promotion and beautification.
(3) Mouth Treatment
The bottle mouth is a key part where the glass bottle matches with the cap for sealing, and its precision and quality directly affect the sealing effect. Mouth treatment includes processes such as grinding and polishing. Through precise processing, the dimensional accuracy and surface finish of the bottle mouth are ensured, so that the cap fits tightly with the bottle mouth to prevent leakage.

5.Quality Inspection: Strictly Controlling Quality
Throughout the production process of glass bottles, quality inspection is carried out from start to finish. From the incoming inspection of raw materials to the performance testing of semi-finished and finished products, there are strict standards and procedures. Common inspection items include appearance inspection (checking for defects such as bubbles, cracks, and impurities), dimensional measurement (ensuring that the height, diameter, wall thickness, etc., meet the requirements), internal stress testing (detecting the magnitude of internal stress in glass bottles through polarized light), compressive strength testing (testing the maximum pressure the glass bottle can withstand), and sealing performance testing (checking the sealing effect between the cap and the bottle mouth).
Only glass bottles that pass all strict inspections can enter the market, providing consumers with safe and reliable packaging containers.
The craftsmanship of glass bottles is a complex technology that integrates science and art. Every link from raw material selection to finished product delivery embodies the wisdom and hard work of countless craftsmen and technicians. With the continuous progress of science and technology, glass bottle craftsmanship is also constantly innovating. In the future, we can expect to see more environmentally friendly, intelligent, and beautiful glass bottle products, adding more color and convenience to our lives.
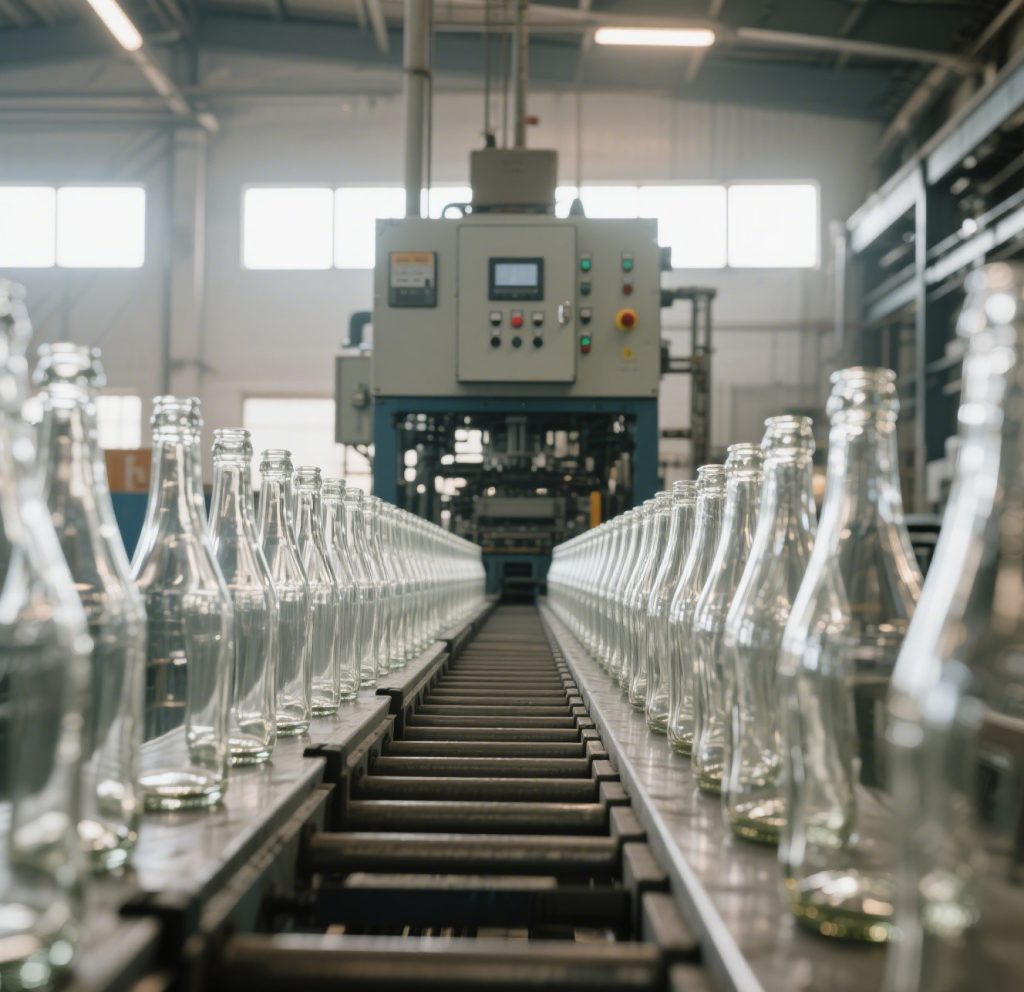