The Production of Glass Bottles
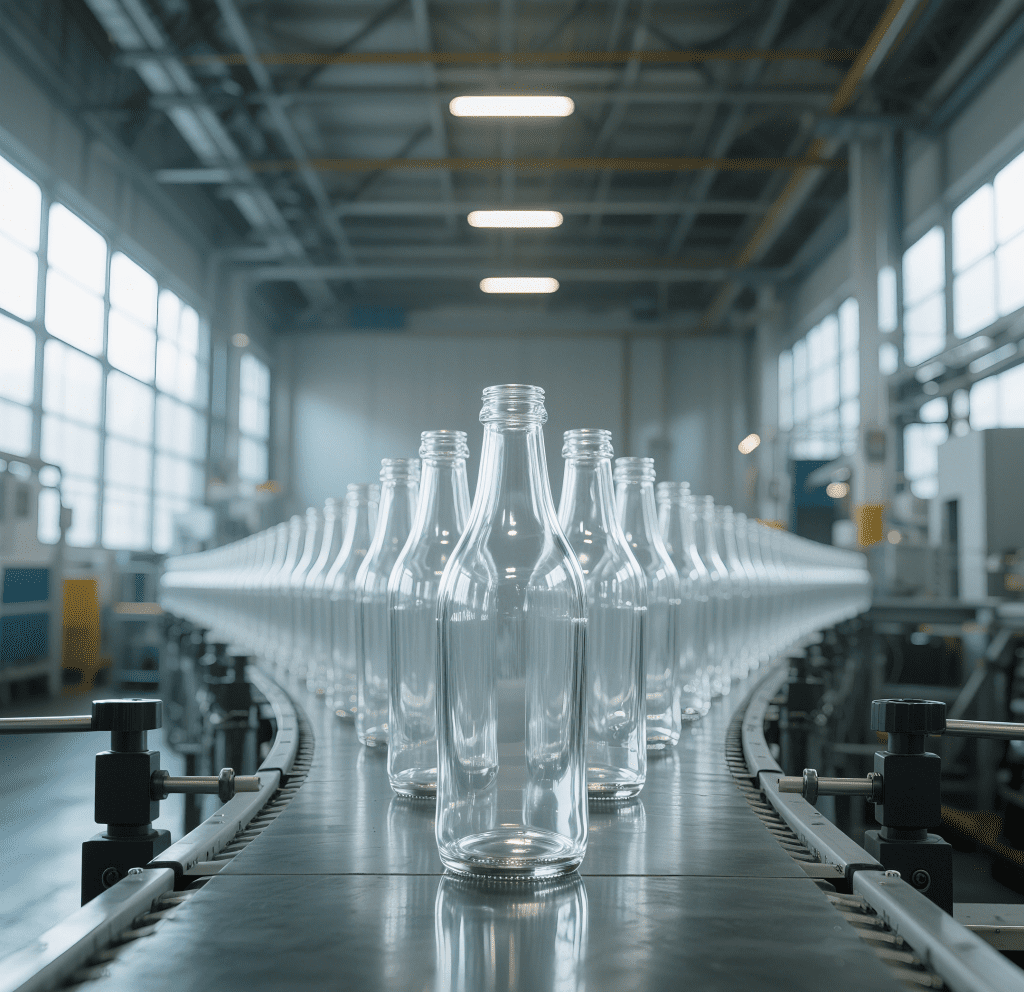
Glass bottles, with their transparency, durability, and recyclability, are widely used in various industries. Understanding how they are produced can deepen our appreciation for these common yet essential containers.
1. Selection of Raw Materials
The production of glass bottles begins with the selection of raw materials. The primary ingredients for making glass include silica sand, soda ash, and limestone. These materials are carefully measured and mixed in precise proportions to ensure the desired properties of the final product. Additionally, cullet, which is recycled broken glass, is often added to the mixture. Cullet helps reduce energy consumption during the melting process and is an environmentally friendly addition.
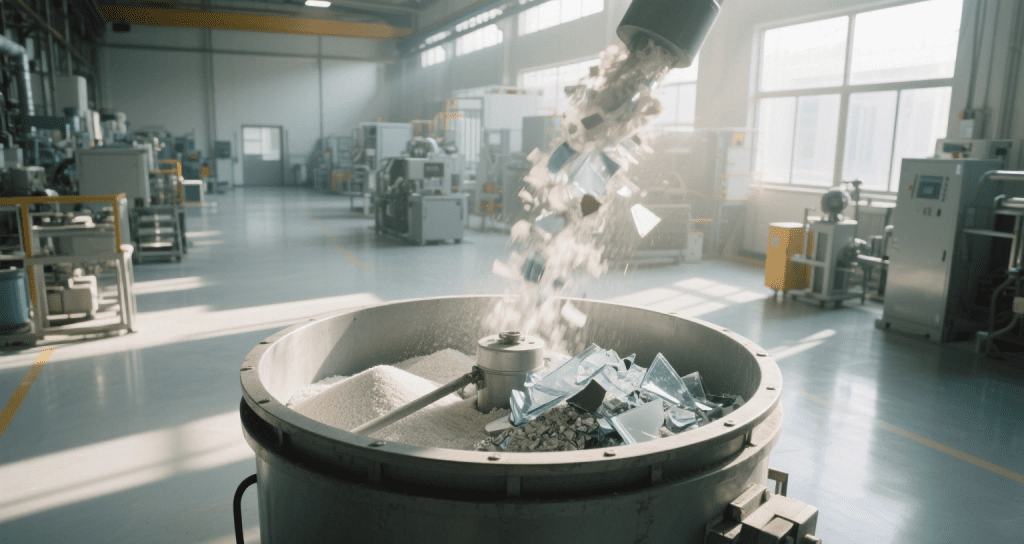
2. Melting Process
The next crucial step is melting. The mixed raw materials are fed into a large furnace, which can reach temperatures of up to 1500°C. In the intense heat, the materials gradually melt and transform into a homogeneous liquid glass. This molten glass is then carefully monitored and adjusted to maintain the right viscosity and chemical composition.
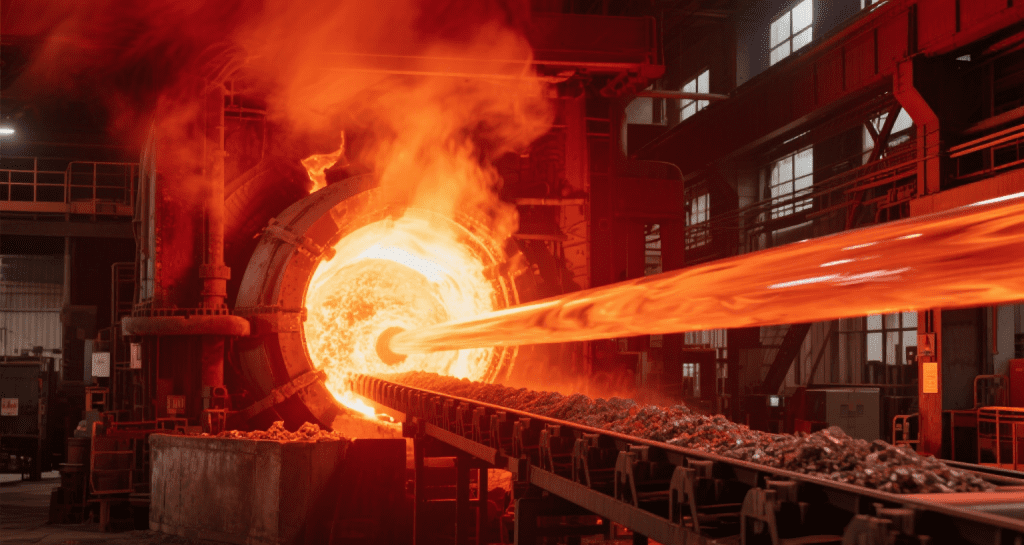
3. Forming Methods
Once the molten glass is ready, it’s time for forming. There are several methods for forming glass bottles, with the most common being the blow – and – blow method and the press – and – blow method. In the blow – and – blow method, a gob of molten glass is first gathered on the end of a blowpipe. Then, it is blown into a preliminary shape in a blank mold. After that, the partially formed glass is transferred to a finishing mold and blown again to achieve the final bottle shape. The press – and – blow method, on the other hand, starts with pressing the molten glass into a pre – shape in a mold using a plunger. Then, it is blown to expand and form the final bottle.
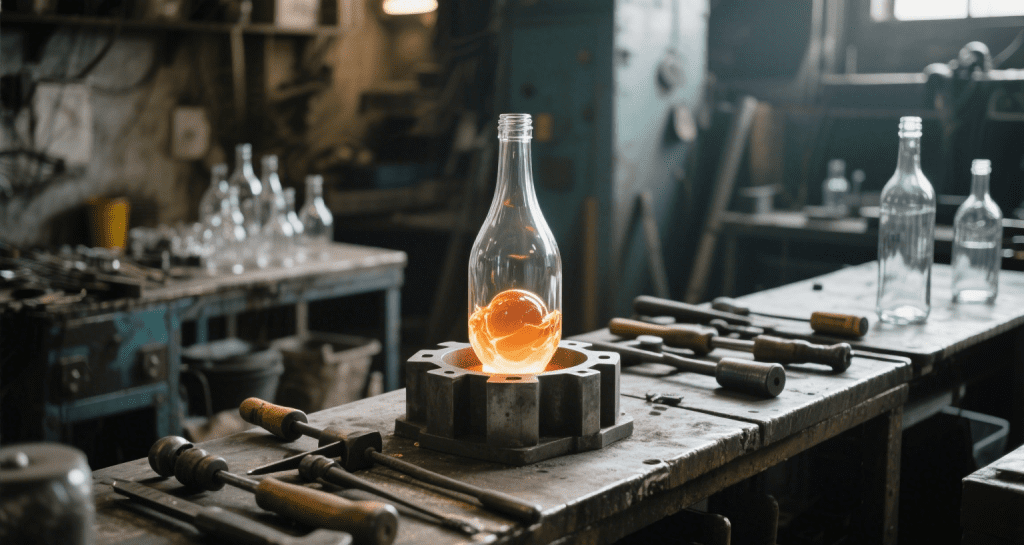
4. Annealing Treatment
After forming, the glass bottles need to be annealed. Annealing is a heat – treatment process that removes internal stresses within the glass. The bottles are slowly heated in an annealing lehr and then cooled down gradually. This process ensures the strength and durability of the glass bottles, preventing them from cracking or breaking easily.
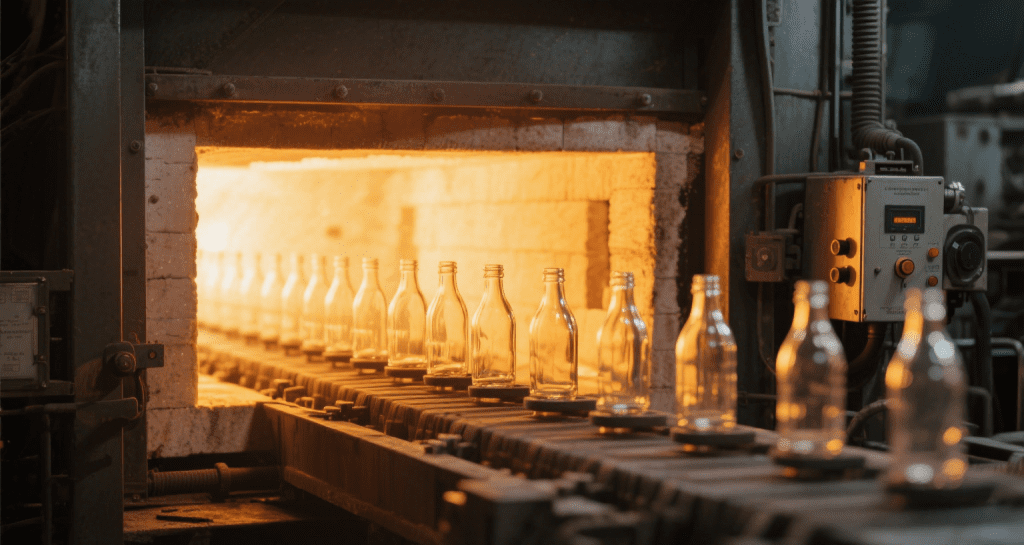
5. Quality Inspection
In the final phase of production, each glass bottle undergoes a meticulous quality inspection process. Specialized equipment and trained inspectors rigorously examine the bottles for imperfections such as cracks, air bubbles, and inconsistent wall thickness. Any bottles failing to meet the established quality benchmarks are immediately removed from the production line. Conversely, the compliant bottles are thoroughly cleaned, affixed with labels, and carefully packaged, ready for shipment to various destinations.
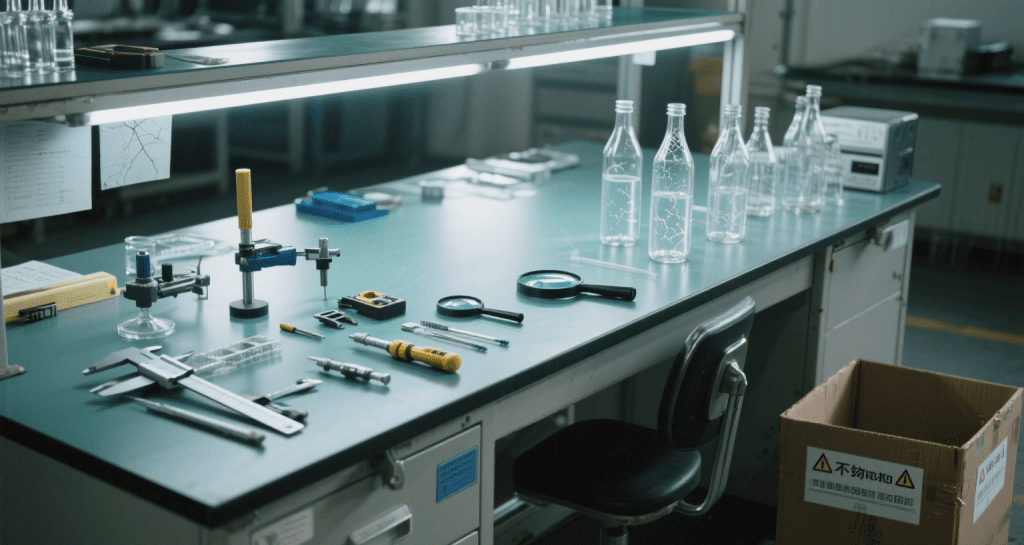