A Comprehensive Analysis of the Volt Processing Production Line: Dual Breakthroughs in Efficiency and Precision
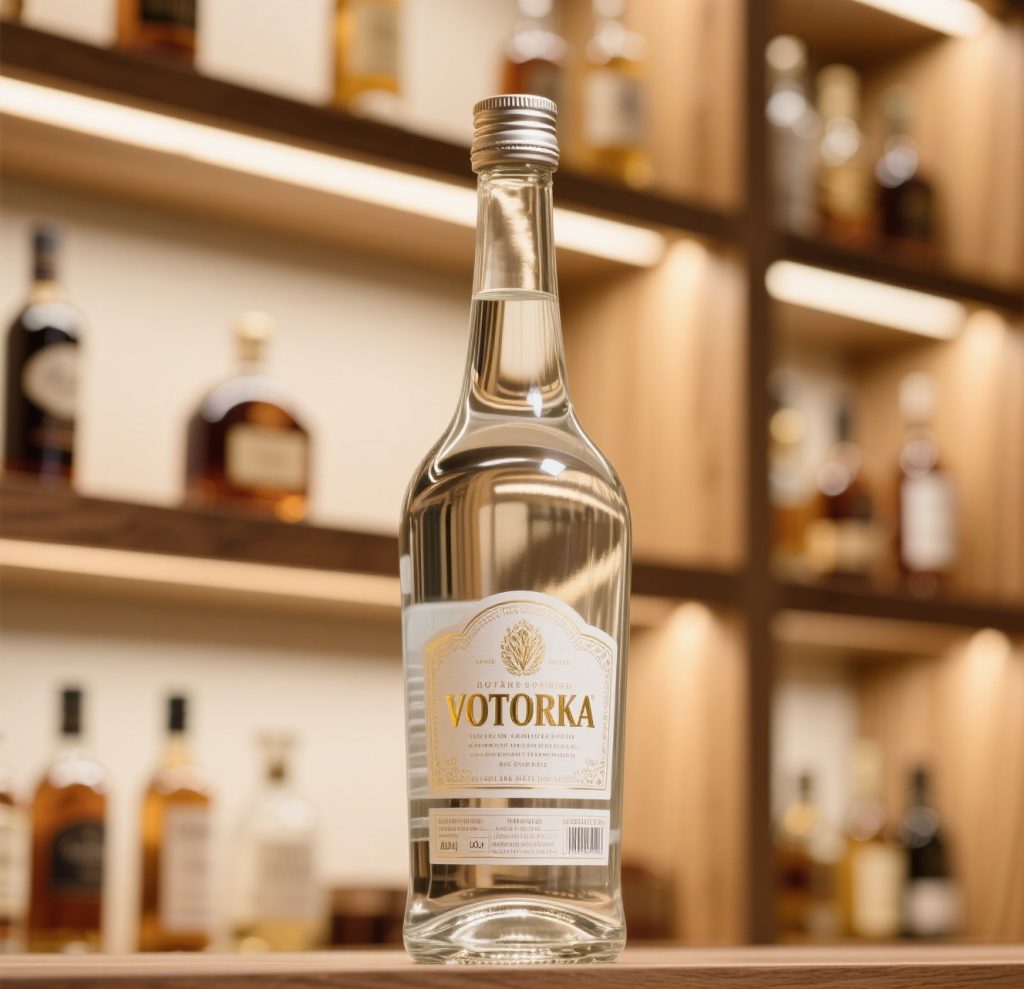
Vodka bottles are usually made of glass, with main raw materials including quartz sand, soda ash, limestone, etc. The quality of these raw materials directly affects the quality of the bottles, so strict screening is required. For example, quartz sand should be pure in texture and uniform in particle size to ensure the transparency and stability of the glass. Before use, the raw materials need to be pretreated: crushing small pieces of raw materials, drying damp and cold raw materials, and removing iron from iron-containing raw materials to ensure glass quality.
Ingredient Mixing
According to the specific requirements of the bottle, the proportion of various raw materials is precisely controlled. For instance, to produce high-quality, highly transparent vodka bottles, the proportions of quartz sand, soda ash, and limestone must be accurately adjusted. During the batching process, some auxiliary ingredients such as yttrium oxide and iron oxide can also be added to change the properties of the glass in the molten state, resulting in glass of different colors.
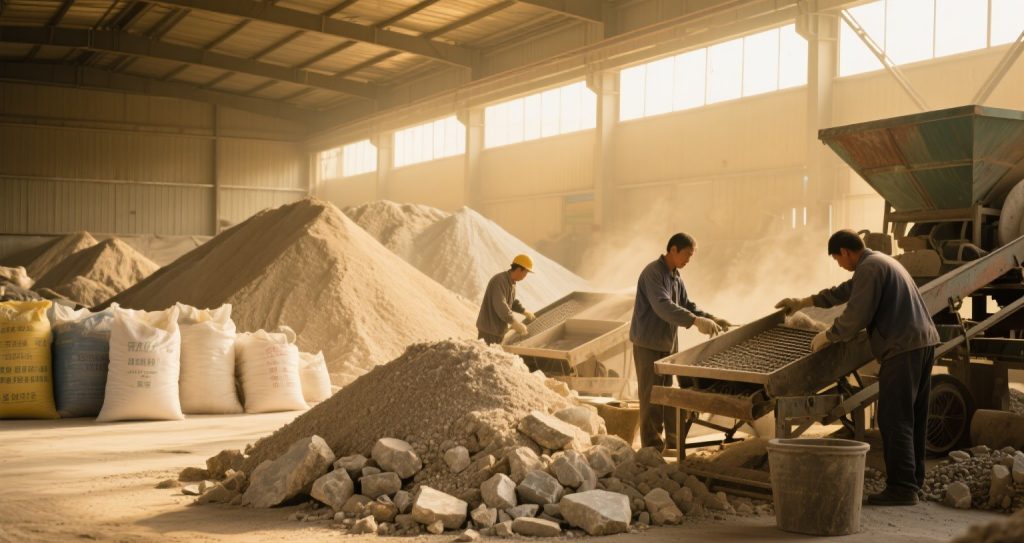
Glass Melting
The prepared raw materials are put into a tank kiln or furnace and heated at a high temperature, usually reaching 1550 – 1600 degrees Celsius. At such high temperatures, the raw materials gradually melt, and after a period of smelting, a uniform, bubble-free liquid glass that meets the forming requirements is formed. This process has extremely high requirements for the temperature control of the furnace; both excessively high and low temperatures will affect the quality and fluidity of the glass.

Molding Process
Mold Making: The bottle mold is made according to the design requirements. The shape and craftsmanship of the mold determine the final shape and size of the bottle. The mold is generally made of metal and needs to undergo precision machining and surface treatment to ensure its accuracy and surface quality, thereby ensuring that the produced bottle has an exquisite appearance and precise dimensions.
Glass Forming: The liquid glass is put into the mold to cool and solidify into the desired shape. Common forming methods include blowing and pressing. Blowing is suitable for making bottles with complex shapes and thin walls; by blowing air into the liquid glass, it expands and takes shape in the mold. Pressing is suitable for making bottles with regular shapes and thick walls; the liquid glass is pressed into the mold by pressure to form. For example, some high-end vodka bottles adopt manual blowing technology, endowing the bottles with a unique artistic sense.
Heat Treatment Process
Annealing Treatment: The formed bottle needs to undergo annealing treatment, which involves heating the bottle to a certain temperature and then cooling it slowly. This process can eliminate the internal stress of the glass generated during the forming process, prevent the bottle from breaking due to stress concentration in subsequent use, and improve the strength and stability of the bottle. The annealing temperature and cooling rate need to be strictly controlled; different thicknesses and compositions of bottles require different annealing process parameters.
Quenching Treatment: In some cases, the bottle will undergo quenching treatment. By rapidly cooling the glass surface, compressive stress is formed on the surface, improving the surface hardness and wear resistance of the bottle. However, the quenching process requires precise control of process parameters; otherwise, defects such as cracks may occur in the bottle.
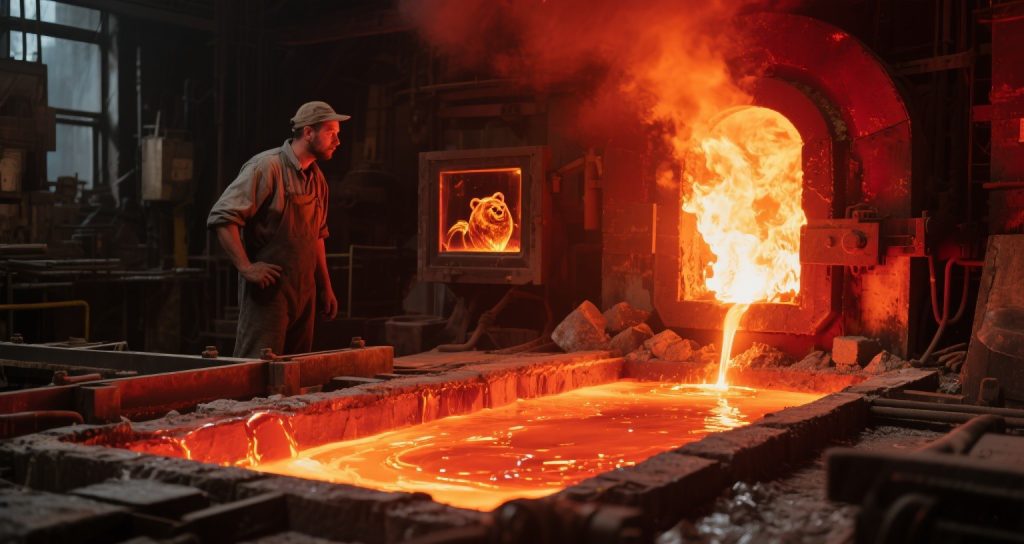
Post-Processing
Cutting and Polishing: The annealed bottle is cut to remove excess glass, making the bottle reach the specified height and bottle mouth size. Then, the cut edges are polished to make them smooth and flat, avoiding scratching users during subsequent use. The polishing process usually combines mechanical polishing and manual polishing to ensure polishing quality.
Surface Treatment: To enhance the appearance of the bottle, surface treatments such as spraying, carving, and frosting can be carried out. Spraying can make the bottle surface show various colors and lusters; carving can form exquisite patterns and characters on the bottle surface, increasing its artistic value; frosting treatment can make the bottle surface have a delicate texture. For example, some high-end vodka bottles use laser engraving technology to carve complex and exquisite patterns.
Labeling and Anti-Counterfeiting: According to brand requirements, labels are attached to the surface of the bottle, which usually contain information such as the brand name, alcohol content, capacity, and origin. At the same time, to prevent counterfeit and shoddy products, some bottles also adopt anti-counterfeiting technologies such as laser anti-counterfeiting labels and QR code anti-counterfeiting.
Quality Inspection
Appearance Inspection: The appearance of the bottle is comprehensively inspected by manual or automatic detection equipment, including checking whether the bottle body has cracks, bubbles, scratches, whether the color is uniform, and whether the patterns and labels are clear and complete. Any bottle with appearance defects will be rejected.
Dimension Inspection: Professional measuring tools are used to accurately measure the height, diameter, wall thickness, and bottle mouth size of the bottle to ensure that the bottle size meets the design requirements. Bottles with excessive dimensional deviations that affect filling and packaging will also be judged as unqualified products.
Strength Inspection: The bottle is subjected to strength tests such as pressure resistance test and impact resistance test to ensure that it will not break during normal use and transportation. By simulating actual usage scenarios, a certain pressure or impact force is applied to the bottle to check whether its strength meets the standard.
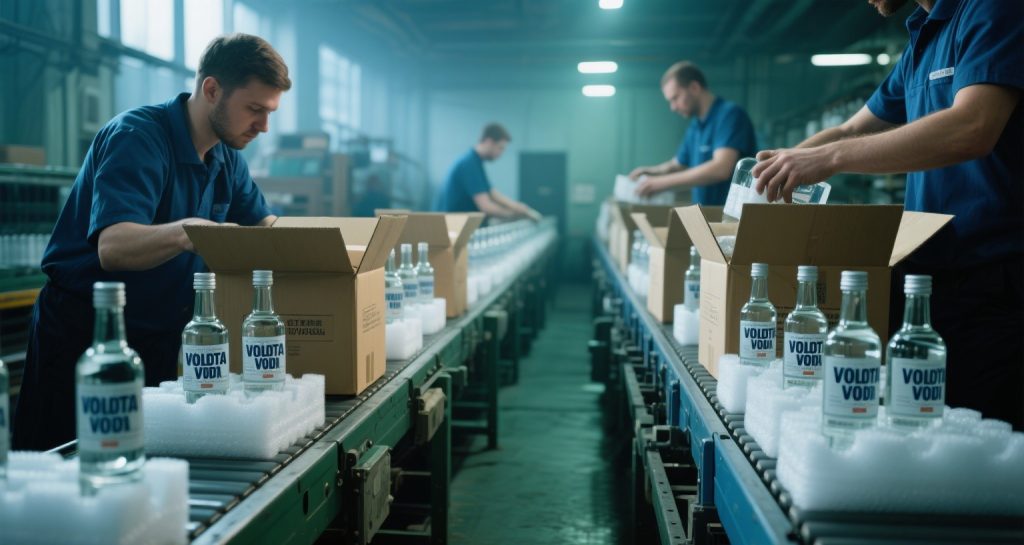
Packaging and Shipping
Vodka bottles that pass the strict quality inspection are packaged and shipped. Usually, packaging materials such as cartons and foam are used to protect the bottles from collision and damage during transportation. The packaged bottles are then transported to wineries for vodka filling and sales.
The production process of vodka bottles is a complex and delicate process. From the selection of raw materials to the packaging of the final product, every link embodies the wisdom and efforts of craftsmen, aiming to provide consumers with practical and beautiful bottles that better showcase the unique charm of vodka.